The Cost of Replacing a Cylinder in a Nissan Truck
Friday, February 28, 2014 | Labels: a, cost, cylinder, in, nissan, of, replacing, the, truck | 0 comments |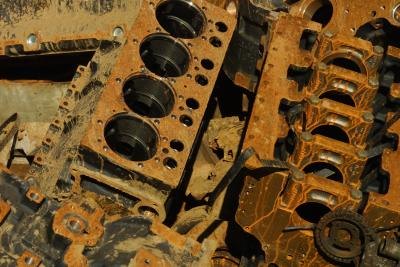
Some Nissan models - particularly the ZD30 Nissan patrol, have had a history of serious engine problems over the years, including piston cracks, head cracks and cracked cylinders and engine blocks. Nissan has taken steps to rectify the issues in recent years. If you have a cracked cylinder, that means that the recess in which the piston slides back and forth has become damaged, resulting in the air/fuel mixture leaking out around the piston. If it is the cylinder that is cracked, rather than the piston, you may have to replace the entire engine block.
Diagnosis and Troubleshooting
A cracked cylinder will generally result in the loss of compression in that one cylinder. You may notice your engine "missing," running poorly and lacking in power. If your car runs at all, you would notice poor acceleration and poor performance on hills. However, there are a number of other issues that could cause this same problem. You may want to check your spark plugs for proper gapping and functioning. Also check your fuel injection system and your head gasket. Each of these items is much less expensive to repair, and would cause similar symptoms, so rule each of these out before replacing the cylinder.
Parts
If you determine that your engine problems are, in fact, the result of a cracked cylinder, and the crack is too severe to weld shut, you will need to replace the engine block itself. The cost of the engine depends on the year, make and model of your Nissan. Expect to pay between $1,800 and $2,000 for a fully remanufactured engine block. However, you may also be able to find a complete engine in the aftermarket for around a thousand to $1,500, depending on the make and model of your Nissan.
Labor
Generally, auto mechanic shops have a shop rate prominently posted in the customer service area. This is the hourly rate that the mechanic charges, generally in addition to the diagnostic fee, if any. The mechanic will give you an estimate based on the shop rate, times a multiplier from an industry guide called "The Mitchell Book" that lists how much time it typically takes to do a repair. Expect to pay between 8 and 10 hours of labor charges to do a full engine swap, depending on the make and model of your vehicle, assuming there are no other repairs to do.
Master Cylinder
It is possible that your mechanic is erring to your master cylinder. The master cylinder converts mechanical energy from your foot pressing down on the brake pedal into hydraulic energy, which is then distributed through the power steering system to your brakes, or to your clutch. You can get a new brake master cylinder for about $100-$120. For clutch master cylinders, expect to pay about $30 to $60 for the part. According to CarsDirect.com, the average cost of a brake master cylinder replacement is $200-$300, including labor.