How to Rebuild Sea Doo Engines
Wednesday, April 30, 2014 | Labels: doo, engines, how, rebuild, sea, to | 0 comments |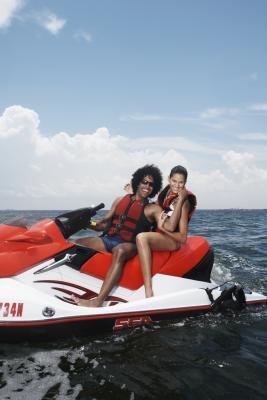
Rebuilding a Sea-Doo engine is one of those tasks that owners hope to avoid during the time they own the watercraft. However, as is sometimes the case with small engine maintenance and repair, an occasional rebuild may be necessary to keep maintenance costs low and to possibly avoid having to replace the entire Sea-Doo before the end of its life cycle.
Instructions
- 1
Remove all wires attached to the outer part of the Sea-Doos head. Use white masking tape and a permanent marker to mark each wire as you remove it from its original location. This makes it easier to replace the wires and put them back where they belong when you put the entire engine back together.
Remove the bolts with the appropriate size wrenches or ratchets. Bolt size depends on the Sea-Doo model you own and its engine size.
2Pry the head open using a flat-head screwdriver. Caully remove the two halves from one another and inspect the interior of each. Examine the inside of each cylinder for signs of corrosion. A corroded cylinder indicates the need for a rebuild.
3Remove the entire engine from the engine block and get it ready for rebuilding. Your best bet for doing this is to send it off to a machine shop to have the cylinders bored, the surface of the block prepared and the stroker kit balanced.
4Set the crank and check for clearance. Begin by unbolting and pulling off the brackets on the top of the block so the tank can be set it in place. Ensure the oil gulley plug is in place. It is located in one of the holes near the corner on the top of the engine block, right next to where the oil filter goes. Place the bearings for the main crank in place by sitting them inside the engine shaft. Lubricate each bearing with engine assembly lubricant.
5Lay the crankshaft in the engine shaft by caully aligning each piece of the crankshaft with the corresponding bearings. Cover the crankshaft with the main bearing caps, which should be bolted into place. Tighten each bolt with a ratchet, but avoid over tightening the bolts.
6Insert the rods and the piston through the cylinders and connect these to the crankshaft using the connecting bearings. Bolt the rods to the bearings on each rod. Test out each rod and piston assembly to ensure that each has proper clearance to move through the cylinder.
7Cut the block where needed to ensure proper clearance for the motor. Install both the cam and the cam bearings once you have the necessary clearance. Install the timing gear on the crankshaft, along with the crank bearings and the timing chain.
8Replace the wires in the original configuration based on your wiring diagram and labels. Replace exterior bolts responsible for holding the engine block in place.